Clemson Vehicular Electronics Laboratory: Brushless DC Motors
Some Known Incorrect Statements About An Introduction to Brushless DC Motor Control - DigiKey
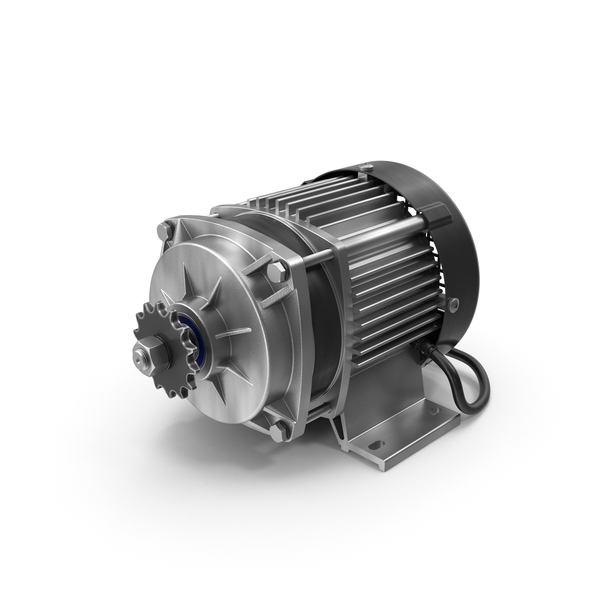
Concurrent electric motor powered by an inverter The motor from a 3. 5 in floppy disk drive. The coils, arranged radially, are made from copper wire covered with blue insulation. The rotor (upper right) has been eliminated and turned upside-down. The grey ring inside its cup is an irreversible magnet.
DC brushless ducted fan. The 2 coils on the printed circuit board engage with six round irreversible magnets in the fan assembly. A brushless DC electrical motor (BLDC motor or BL motor), also referred to as an electronically commutated motor (ECM or EC motor) or simultaneous DC motor, is a concurrent motor utilizing a direct current (DC) electric power supply.
The controller changes the phase and amplitude of the DC existing pulses to manage the speed and torque of the motor. This control system is an alternative to the mechanical commutator (brushes) utilized in many traditional electric motors. The building and construction of a brushless motor system is normally comparable to a long-term magnet synchronous motor (PMSM), however can likewise be a changed unwillingness motor, or an induction (asynchronous) motor.
What Does Brushless DC motor (BLDC) - controller and driver - Infineon Mean?
The benefits of a brushless motor over brushed motors are high power-to-weight ratio, high speed, nearly instant control of speed (rpm) and torque, high effectiveness, and low maintenance. Brushless motors discover applications in such locations as computer system peripherals (hard disk, printers), hand-held power tools, and cars ranging from design airplane to cars.
Background [modify] Brushed DC motors were developed in the 19th century and are still common. Click Here For Additional Info were enabled by the development of solid state electronic devices in the 1960s. An electric motor establishes torque by keeping the electromagnetic fields of the rotor (the rotating part of the machine) and the stator (the fixed part of the maker) misaligned.
DC going through the wire winding develops the magnetic field, offering the power which runs the motor. The misalignment generates a torque that attempts to straighten the fields. As the rotor moves, and the fields come into alignment, it is essential to move either the rotor's or stator's field to preserve the misalignment and continue to create torque and movement.